It's been a few weeks since I've updated the journal. (Hope everybody had a great holiday!) Here's what's been going on...
HVAC - Good Lawd, the installation is moving slowly! It's been 30 days now and they're finally getting close to completing the upstairs duct work. The upstairs air handler has also been installed. Hopefully this week they'll get started on the downstairs system. Back when we had no heat, the HVAC salesman actually told me that the installation would take about 3 days. Ha!! Most days there's only been one young guy here working alone. Sometimes he has another guy helping. The good news is that they're really not holding anything up.
Electrical - I think we're getting close to our rough-in electrical inspection. It also looks like we're going to have to step up to 600 amp service because we have decided to install two electric tankless hot water heaters. They each draw a maximum of 80 amps which pushes us over the top for 400 amp service. (The water heaters are phased, so they would rarely actually pull the full 80 amps.) We're waiting on the electric company to come out so we can see what our options are.
Siding - Many weeks and many delivery dollars later, the siding is finally here.
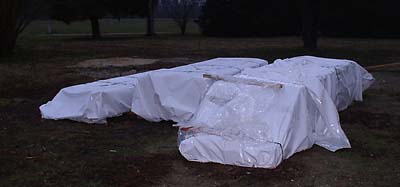
I had the siding primed and painted by Carolina Colortones near Asheville, North Carolina. Then we couldn't find a flatbed to bring the siding to us. Finally, $$$ later, we had a truck and driver. But because the siding needed to be offloaded with a forklift (which we don't have handy here at the house) I had to ask the local lumberyard that we've been working with if we could have the siding delivered there and then pay them to bring it to us. So, it's finally here. But even with all the delays, I'm not really ready to start hanging it. I need to finish casing the doors, install the corner boards, trim out the screened porch, etc. At this point, I'm thinking that my best strategy might be to focus primarily inside during the remaining cold winter months and then turn my efforts back outside in the spring. I don't think any harm will come from this since we're watertight and sealed in house wrap.
Speaking of corner boards and such... I'm having a heckuva time getting clear cedar from the lumberyard. My first order was several months ago and I got beautiful clear cedar. Really nice stuff. Ever since then, every time I order clear cedar surfaced on all sides, I get stuff that looks like this.

Full of knots, it's unusable for my purposes. Or, in the case of the 7/8" X 8 board on the right, it arrives rough on all sides instead of surfaced. I think I'm going to need to find a new supplier for cedar.
Exterior Doors - This weekend I re-trimmed the rear garage door that was delivered with standard brick moulding so that it will match the other doors.

I also built the jamb and trimmed out the rear door of the colonnade. The door (recycled from the kitchen we tore down) isn't really hung yet as we try to decide what hardware we want to use.
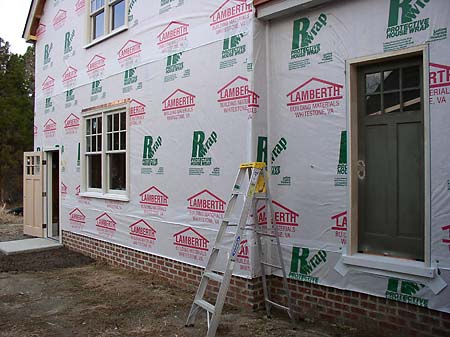

Progress is slow on jobs like this because (a) I'm slow and (b) I have to stop and back-prime everything and then wait for the primer to dry, which isn't fast when it's cold. Also, I am taking the time to go ahead and fill all the nail holes as I go. So when I'm done with a door or window, it's ready for paint without any further prep.
Oh, and the other reason that I'm slow is (c) every time I finish a project I have to spend 10 minutes marvelling that I actually did this by myself and then (d) another 10 minutes showing it off to Gay and William and coaxing compliments from them. It does slow things down...
For the colonnade door I want to build steps like these.
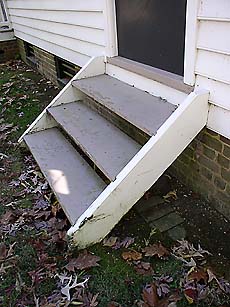
I'm not sure if I the building code will allow us to get by without a handrail though.
Today I started work on the jambs for the front and back center hall doors.

I began with the new pair first since they're nice and square. We have decided to put the new pair on the back and the old pair, with all of their old character, will go on the front to make a statement to visitors. I hope to receive the 10-inch HL hinges for these doors later this week. These hinges will be appropriate and also make the doors easier to hang than with butt hinges. We can't wait to see them installed.
Framing - We still haven't had our framing inspection because of some chicken-or-the-egg scenarios. I needed the electrican to replace some old wiring below the floor of William's future bathroom before I put down the new subfloor and then built the last wall for that room. He worked on that today and will finish it tomorrow morning, so then I'll be good to go.
Gay's been pitching in when she has time, like getting the old double doors ready for priming and priming endless feet of other lumber. Several weeks ago she even braved standing on a ladder on the porch roof to hold the end of a soffit board for me!

We took time out on New Year's Eve for a nice dinner at a nearby, restored, 18th century tavern...Hughlett's Tavern. Gay and William commented on how we can't go anywhere like this anymore without me scrutinizing the critiquing the trimwork.

That's all the news that is the news. -- Bill
I forgot to post photos of our Christmas tree last month. Because all of our stuff is in storage during construction, we decided that we would buy a fake tree (this year and this year only!) and make our decorations out of construction materials.
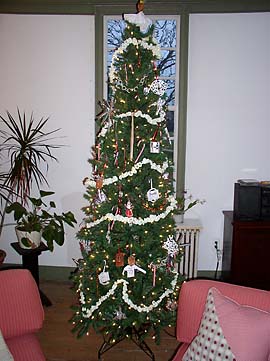
From a distance it looked pretty typical. But up close it starts to look a little different, like with strung packing peanuts (from an order of restoration glass) and a copper chain.

A Santa that William carved from a shim...

And I'm not sure what to say about this thing...an applehead, some copper, some HVAC insulation, and white wire for teeth. Some kinda twisted angel maybe?
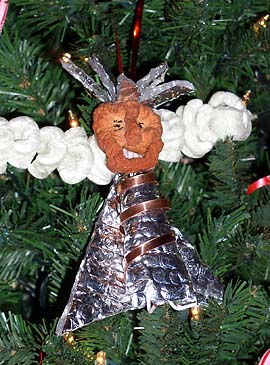
Anyway, we had fun decorating.
The electrician replaced the old wiring under William's porch floor yesterday so I have been able to move forward in there, putting down the subfloor and moving along with the framing.

I'm building the partition wall in place instead of building it on the floor and then raising it. Partly because of limited space, but mostly because the floor slants so every stud is a different length. It's just easier to go on and build it in place, although slower.
I think this quirky little bath is going to be very cool. The design has changed many times as we tried to figure out the best configuration for the long, narrow space.

The sink is going to go in this little corner. We found a cool corner sink that fits perfectly.
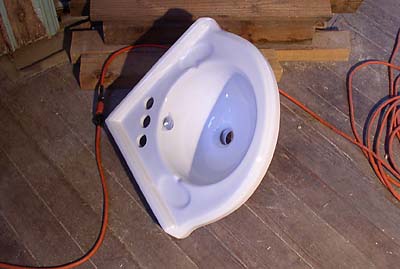
I should have this finished tomorrow. One step closer to our framing inspection! -- Bill
Yesterday we made another pilgrimage to Williamsburg to look at exterior colors. We carried around our fan pack of Williamsburg colors and tried to identify the colors that we liked while William recorded everything in his journal.
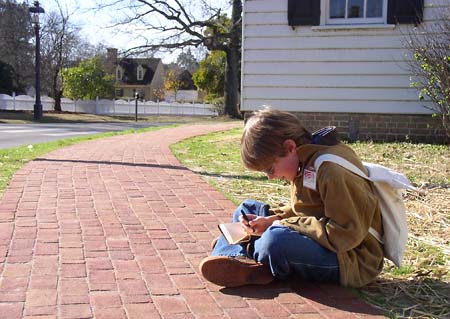
At the end of the day we had a pallette of about 5 colors that we all liked. Now, we just need to determine which of these colors we use and where.
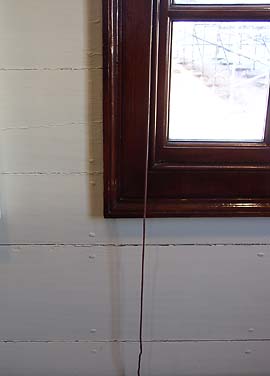
This is an example of how I want to treat the main wall in the new family room...mixed-width horizontal shiplap boards faced nailed with cut nails. We probably won't be able to go as wide as these ($$$), but hopefully we can create the same feel.
The nailheads in the photo above are making me flash back to last week. It was the week of "people who just don't get it." Like the guy who stopped by wanting to know if he could give us a price on hanging our siding. When I explained that we wanted the siding face nailed with cut nails and showed him an example on the Dutch Colonial that I did a couple years ago (with nailheads showing like in the photo above) all he could say was, "it's sure not pretty." Then there was the guy who stood in the new center hall and asked me if we are going to be putting sliding glass doors in the openings where our double doors are going. ("Uh, no...") And the phone guy who asked me if we were going to be replacing the cypress shingles (5 years old) on the Dutch Colonial. And the HVAC guy who assumed that we would be taking down the beadboard ceiling in the law office. ("Oh...you're just gonna paint it?") It was a trying week.
While in Williamsburg yesterday we also knocked out a lot of our key lighting purchases...all of the exterior door lighting and the kitchen lights. We found everything at The Lamplighter Shoppe. The photos on their Web site really don't do their products justice. In fact, we never would have purchased the lanterns that we did if we were just looking at the Web photos. But they really have a great selection are very helpful and knowledgable and do a lot of work for the Colonial Williamsburg Foundation. It was a great feeling to get those decisions behind us. I'll share photos of our selections when they arrive.
The framing in William's room is done now.

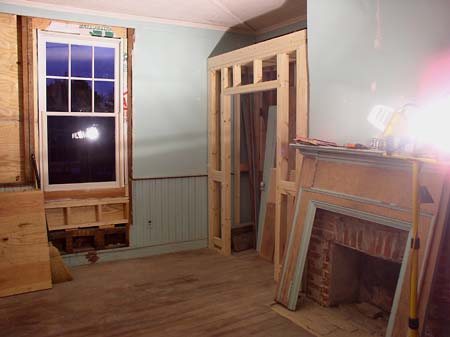
I didn't take William's closet all the way to the ceiling so that we wouldn't lose another corner of the beadboard ceiling. (Yes, we're keeping it.) Now William thinks that he might want to sleep on top of his closet. ("Uh, no...") -- Bill
We passed our framing and chimney inspection this morning! So far, we're batting 100% with our inspections. We should be ready for our electrical inspection in the next week. Then we can get going on insulation.
The weather this week is unseasonably warm so we've turned our attention outside. Today we started working on the master bedroom's screened porch.

Gay's great at any job that involves wrapping something, so I asked her to flash the top of the half wall before I install the whiskey rail on top of it. Meanwhile, I started working on boxing in the posts. -- Bill
I've been scattered between several projects lately.
Today I trimmed out the back door, inside and out. The 3-part trim is modeled after this door in Williamsburg and is 6-1/4" wide.

We've also been working on the screened porch in fits and starts.

Our rough-in electrical inspection is scheduled for Thursday. -- Bill
Ugh, I probably won't be able to walk tomorrow after spending the entire day crouched in the attic above the old law office.
In this space there was a heavy metallic paper covering the joists for insulation purposes.


Being metallic on both sides, I assume that the theory was to keep inside heat from escaping through the beadboard ceiling and to keep outside heat from radiating through. Well, in the course of the electrician, plumber, and HVAC guy doing their work, the paper got pretty destroyed. And actually, I had always assumed that there was also insulation under the paper...which there wasn't.
So when we woke this morning to a torrential downpour, I figured this was a good day to clear out the old paper to make way for proper insulation. Then once I pulled the paper out, I decided that I might as well clean things up more to get rid of years of dirt, old roofing debris, and mud dauber nests.

Since there is no way to get a ShopVac up there, this meant crawling around on my hands and knees with a dust pan and small brush and a passel of plastic leaf bags. It may seem pretty anal to go to this length to clean up a space that will be unused and is not even easily accessed. But my thinking is that all of this dirt could possibly sift down through the beadboard ceiling over time, as well as provide mouse bedding. Plus, with everything cleaned up I can get an exteriminator to come and give everything a good treatment before we insulate. I did find two small instances of active powder post beetles, otherwise everything looked great.


Now, it's spic and span, and I can no longer stand upright.
The electrician is still working on the panels, so we've delayed that inspection until Friday. The two electric tankless hot water heaters have really added up to a lot more work since they bumped us up to 600 amp service. They better be worth it!

And exciting news! Today we broke down and bought a really cool antique mantel for the new family room.
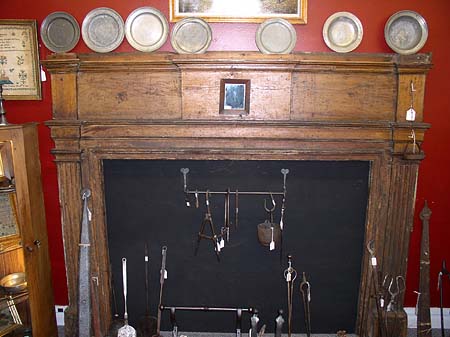
We discovered it months ago and haven't been able to shake it since. Especially since the opening is the perfect code-required size for our firebox! It has patina out the wazoo, but also needs some work. The top shelf is missing, so I'll need to find some matching old wood to make something. We think it'll really add a lot of old character to the new family room. -- Bill
It's not good when your workday ends with you pacing back and forth in the backyard, holding both hands over your head (one squeezing the other with a death grip) while swearing repeatedly. But I get ahead of myself.
The day started well when we passed our electrical rough-in and electrical service inspections.
After that I spent the day tackling a dreaded project. The north wall of the law office has so many levels of lumber (old and new) that it undulates from top to bottom and side to side with no two studs being on the same plane. I've been putting off leveling the wall to accept beadboard on the bottom and blueboard on the top, but needed to get this done before we insulate. Slowly, but surely, I made good progress and the bottom area is now leveled and ready for beadboard.
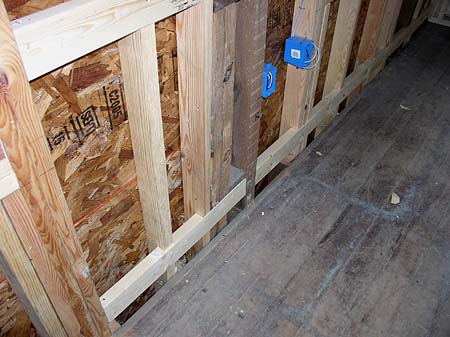
I was going nuts trying to shim and block until I finally decided that perhaps I could do it all at once. I notched a single 2X4 to do both jobs and it worked great.
Around 4:30 I was ready to wrap things up. My last step was to shim an old stud out 1/4". I switched to the nail gun loaded with finish nails and held the shim in place to shoot two nails into it. One. Two. Yeow!! (Well, I didn't yell "Yeow," but you get the idea.) The 16 gauge wire nails (I know, I shoulda bought the 15 gauge gun) sometimes decide to follow the grain of the wood, sometimes going into the wood and then making a 90 degree turn to emerge out the side. Which is where my finger was. I have never felt such pain and was quite sure that my fingertip had been blown apart. Gay heard my yelling and came upstairs.
"Are you bleeding?"
"I'm sure I am."
"Hold your hand above your head."
I'm stomping madly around the law office, hands above head, and swearing.
"Let me see it."
"No." I'm afraid to release my finger from the death grip and discover the extent of the damage. The pain is still excrutiating. I start heading down the steps and Gay follows.
"Can you turn off the compressor for me?" I ask. (Gay and William still think it's funny that I was so concerned about turning off the compressor in the middle of all this. But it's just part of my end-of-the-day routine. And the day was definitely over.)
By now I'm stomping around the backyard, still swearing. Gay comes out of the house with a clean cloth and we're ready to assess the damage. Slowly I ungrip my finger and instead of blood squirting to the sky, I see a small puncture and a couple drops of blood. I turn my finger over, looking for the exit wound. There's none. That's it? Very unimpressive given all the pain. I have no idea how far the nail went in, but it sure hurt like hell. Today my finger is purple and swollen. And very sore.
We'll just call it a gentle reminder to me to be more careful. And yes, my tetanus shot is current. (Thanks to Don.)
Our first expenditure when we started the addition should have been a pickup truck. Gay's van is getting a regular workout hauling lumber and I'm getting a workout pulling the seats in and out all the time.
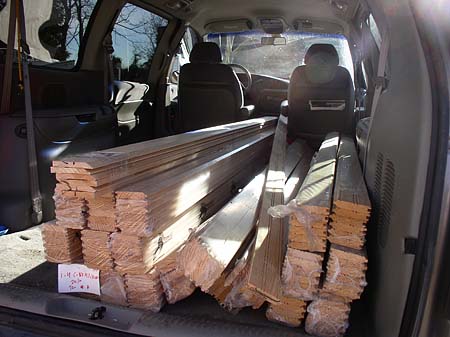
This load is beadboard for the screened porch off of the master bedroom and for William's bedroom.
Today, the three of us worked together to install the beadboard on the screened porch ceiling. It's our first finish surface in the addition!

The ceiling width is 8'-3" so we were able to use 8' boards with no cutting. The bed moulding will cover the gap on each side. This made the job move pretty quickly. Gay worked on a ladder on one side, and I worked on the other...nailing very carefully with fingers all clear. William's job was to keep the boards coming. This was slowed somewhat by him having to write something (poems, riddles, deep thoughts) on the back of each one for posterity.
The chatter winds up getting pretty silly when we work together. And foreign accents somehow become a necessity. "Board" became "Bjord", which evolved to William being "Bjordie." The Swedish board boy. Perhaps I've shared too much. -- Bill
I was back working in the law office today, leveling old studs with new studs.

After removing all nails, I used a power plane to take care of old studs that stuck out too far. It made the job so fast and simple. I love this tool!

So I think this room is finally ready for insulation and blueboard. I can't believe the amount of lumber that I have had to pump into this room just for nailers. I swear, I think 15% of the lumber in the addition is there for the sole purpose of having something to attach the blueboard to. There has to be a better, more ecological way than wasting all that wood.
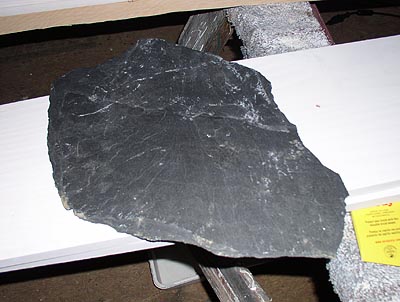
We received a sample of 1/4"-thick slate from Buckingham Slate today. We're looking for irregular shaped slate that we can thinset in the colonnade, laying it just like tile. This sample has one pretty smooth side, and the other side has the natural slate clefts. It looks good, but I'm a little leary about how well it will work for thinset. I need to do some more research and see if I can find somebody who has actually done this.
About six weeks ago I was researching thresholds for the exterior doors that I built jambs for. I really wanted to go with an oak threshhold with a rubber gasket, but couldn't find the gasket anywhere in lengths longer than 3 feet. But our center hall double doors are 4 feet wide. Even the manufacturer Web site only listed 3-foot lengths available. So I sent them an E-mail, asking how I might get longer lengths. Six weeks passed and I never got a response. Today I opened the mailbox and found a fat envelope from M-D Building Products and inside were two 6-foot lengths of the gasket! No note. No invoice. Just the gaskets that I needed! Wow! Thanks!! -- Bill

Agnes Slate Hathaway
1913 - 2006
We were saddened today to hear that Agnes Hathaway passed away. She and her husband Henry Hathaway were the last Hathaway owners of Enon Hall before deciding to sell the farm in 1939. Agnes actually lived here when she was a teenager and her parents were running the farm for the Hathaways. (Henry's father, Walter, died when he was very young and Henry was sent to live with an aunt. The Slates lived here during that time.) When Henry was a young man he returned to Enon Hall and he and Agnes wound up marrying.
We only met Agnes once, back in 1999. Although she freely admitted that she didn't like living at Enon Hall, she generously shared her memories and old photos with us; many of which are on this site. We appreciated the way that she welcomed us into her home as distant cousins of her departed husband. When we told her that we were buying Enon Hall, she just shook her head in a way that said, "Why in the world would you do that?" We have since had nice visits with two of her daughters here at the house and look forward to meeting the rest of our cousins at the service tomorrow night.
Changing gears...
I don't think I've posted a photo of the W&H Moulder in action before.
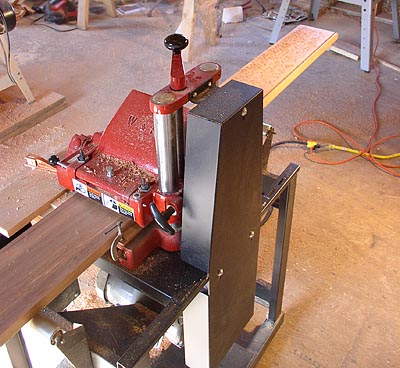
Here it is putting a nice 5/8" bead on a piece of redwood destined to be a part of the front door trim. This is a great little machine!
Speaking of doors, the HL hinges for the center hall doors arrived yesterday from Nathan's Forge and are going to look great on our doors.

We had to stand a door in place to model them. The door looks short because the threshold isn't in. I made the threshold today, so we might actually get these doors hung this week.
Why am I trimming out the doors before we have walls? Good question. This is the way it was done in the old days of lath and plaster. The trim went on first and then the walls were plastered up to the trim. We are doing the same thing with the blueboard plaster veneer system. It also allows you to have nice beefy trim without it sticking way out from the wall.
The heat pump units arrived today.

The pest guy came and treated the attic above the law office. He commented that everything looked "real clean." I'm not sure if he was commenting on a lack of insect activity, or the nice job I did cleaning up up there last week.
I'm a little freaked out to look at the calendar and see that January is almost over! So much work left to do and the time is just flying by while we move at a snail's pace. Looking back, it doesn't seem like we've accomplished much at all this month. We'll have to shoot for a big finish in the final week! -- Bill

We try to keep construction from entering our living space, but sometimes it does. These doors wound up inside late last week for painting and some epoxy work. The epoxy doesn't set up well in the cold, nor does latex paint.
We think we have a color for our new center hall doors. It's Everard Washboard Brown. (It's actually almost the same color as the old redware pitcher that I found in the chicken house last week.) The "brown" has a lot of red in it. And it's one of those colors that changes throughout the day as the lighting changes. Sometimes it gets downright plum, but we like it.

We put one of the doors in place to see how it looked with our trim selection...Pelham Gray. (Which has a lot of green in it.) We like it! (The door is wrong side out in the photo. Gay just painted the inside first. The outside of the door has raised panels.)
The last time we visited Williamsburg we noticed that they paint all of the door sills the same color, on all the buildings. We used that color on our sill too.
We're thinking that we will paint the other exterior doors Pelham Gray and leave the trim on those doors white. This will help to identify the double doors as the main doors and the others as secondary. We have another color selected (James Getty Green) that we think we will use on the shutters.
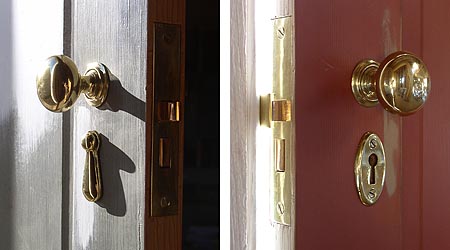
I installed my first mortise lock in the back door. While I was busy drilling and chiseling, the HVAC guy pointed out that "they have a tool for that." Yeah, I know. But I wanted to see if I could do it by hand. It took a little while, but came out well. These mortise locks are from the 1920s and I bought them from Ed Donaldson. He has an amazing inventory of antique and reproduction door hardware. I'm sure we'll be calling on him again.
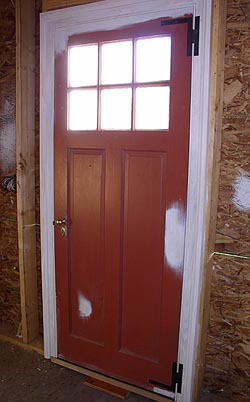
So the back door is now done, other than painting. One down...

Yesterday evening we enjoyed a little bonfire, burning wood scraps from my workshop. I've been keeping a bucket for untreated, unpainted scraps just for this purpose. About two hours of fuel. I couldn't help estimating the cost of each piece as it got tossed to the flames. "Let's see, at 85 cents a foot, that's another 40 cents..."
Today William and I spent the morning under the addition doing some prep work before the vapor barrier goes down. He cleaned out two leaf bags full of trash and scraps left behind by the plumber and HVAC folks. Meanwhile, I spent all morning on my stomach digging a trench under the main heat/AC trunk. There was only 8 inches of clearance below it which left 75% of the crawl space inaccessible. So I dug, and dug, and scraped, and scraped until finally there is enough room for an average size person to crawl under the duct pretty easily. I have a new appreciation for those guys on Hogan's Heroes! Tunneling in tight spaces is hard work! (Not to mention the Mexicans and their border tunnel!) -- Bill
|